An interview with Professor John Nicholls on receiving his lifetime achievement award at Cranfield
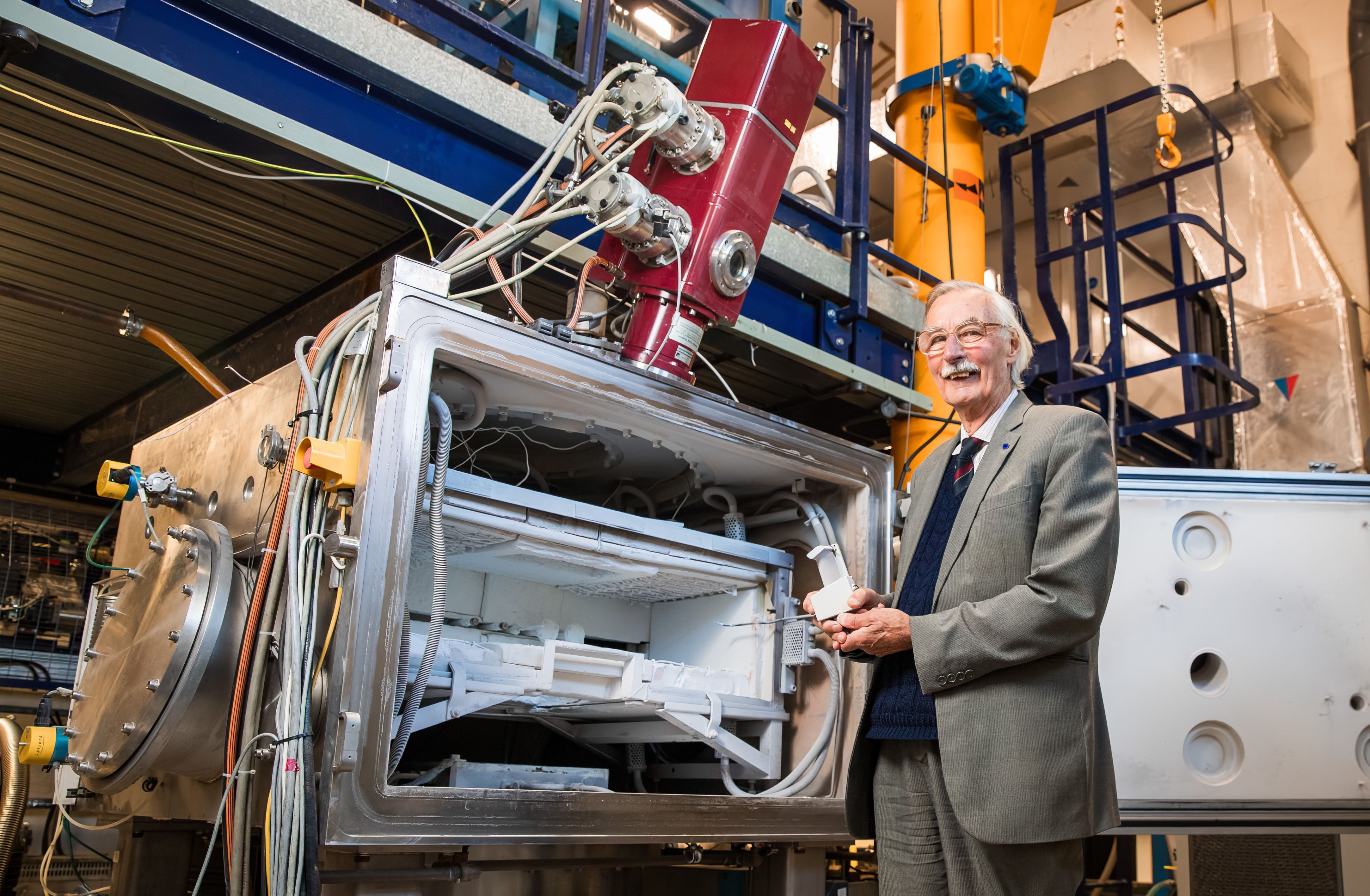
John Nicholls, Professor of Coatings Technology at Cranfield University, and part of the senior leadership team at Royce at Cranfield, has been honoured with a lifetime achievement award at an event celebrating the incredible breadth and impact of his research carried out over his 50-year career so far at Cranfield.
To complement this award and to pay tribute to John’s academic contributions, we interviewed him and asked him about some of his career highlights, current and future projects and his love of scuba diving!
Can you tell me a bit about your specialist subject and area of expertise?
I'd say it's high temperature surface engineering, but in actual fact, what it really means is designing high temperature protective coatings for use on gas turbine engine components.
Gas turbine engines used within aeroplanes run at combustion temperatures of about 1,500°C. The metal that they're made from melts at about 1,300°C. So effectively without the protective coatings, the engine would melt. We design the protective coatings.
So, what does that mean for me? I'm a material scientist. I actually trained as a metallurgist but very quickly moved into being a ceramicist and devising and designing ceramic systems - building a combination of metal and ceramic layers and multi-layers to resist high temperatures.
Our work falls into a number of areas, including research on thermal barrier coatings, or TBCs.
This is a ceramic coating, deposited on top of a metallic coating, deposited on top of a turbine blade, so it's at least a three-layer system and we're looking at building even more complicated structures.
Can you tell me about some of the different companies and industries you have worked with during your career? Have the types of companies you are working with changed?
The first thing I had to do after joining Cranfield was to look at making coatings that were more corrosion resistant so that I could increase the life and the durability of engine parts.
One of my earliest contracts was with Rolls-Royce, back in around 1978-80, and we built oxidation or corrosion protection coatings for them.
Having a foot in the camp of Rolls-Royce, with a confidentiality agreement between them and myself, immediately allowed me to know the problems that they couldn’t release to other people and got us involved in a loop of scientific design which, in turn, gave us new ideas, science and challenges for my students. Once completed, this ended up with the creation of a new coating for Rolls-Royce which therefore helps the UK economy and the whole system.
The challenge, the design, the working with the students, the putting it all together, the feeding back into industry is what motivates me.
The companies we have worked with have definitely changed over time, but all have had a similar requirement and ethos.
I've worked with aero engine manufacturers, alloy designers, steel makers, diesel engine manufacturers, both marine and industrial, racing cars, automotive but all of them wanting to use various materials at different temperatures within their engines and looking at understanding the corrosion damage and the corrosion protection that goes with it.
What do you think has been the key to building these successful, long-term industrial collaborations?
You need to be totally forthright. You need to be able to work with industry, discuss their programmes and problems to help them come up with a design and solution, but keep that information totally confidential.
You have to be able to convince industry that they can trust you enough so that they can tell you their issues and details, related to problems that may be happening, knowing that they absolutely trust that you will not disclose it.
On the basis of that, you can then build a team where you can carry out the research in the university and transfer these ideas into industry as part of a collective team.
You have worked at Cranfield now for over 50 years, can you tell me what research or projects you are most proud of during your time here?
Probably the collaborative work with Rolls-Royce, and particularly Dave Rickerby who was then head of surface engineering at Rolls-Royce, to introduce a new thermal barrier coating for them.
It's called a low thermal conductivity thermal barrier coating, which is a mouthful, but if you look around my lab, it's the pink thermal barrier coating (TBC) and people have recognised me for being involved in the design of the pink TBC.
We worked with Rolls-Royce, designed the TBC, designed the metal coatings underneath it to bond it all together as a system. We then coated turbine blades, Rolls-Royce tested them in an engine and they're now flying on the Trent engine. So, if you sit on the runway on a Boeing 787, the big engines on the wing are Trent 1000 engines and the coating I was involved in the designing is on those engines.
I was very much part of the team that did it - it was a team invention. It wouldn't have got on to the engine without working very closely with industry and it wouldn't have happened without my researchers contributing to it.
Now we've done it, it makes the engine more efficient, therefore it saves carbon dioxide. It probably saves each airline company running that suite of engines something like £25 million a year in fuel savings - so it's a big difference.
As a result of that, I was elected to the Royal Academy of Engineering, which is the top engineering fraternity in the UK, in 2009.
In that same year, I was elected as chair of the Gordon Research Conference in the US, the most prestigious conference of my peers in in this sector and then, in 2010, I was the first recipient of the Tom Bell Medal from the Institute of Materials, Minerals and Mining - all of which felt like really great achievements.
Professor John Nicholls with an example of his renowned pink thermal barrier coating.
Professor John Nicholls with an example of his renowned pink thermal barrier coating.
What is it about Cranfield that means you have stayed working here for your whole career?
It’s a typical one really - I like the university. I like the fact that it's entirely postgraduate which allows us to be very much more focused on our research and our industry.
I like working with industry and having a foot in the door with industry allows me to understand the issues affecting them and allows me to set the challenges for my postgraduate students.
Other than that, nobody has told me that I can't do anything.
I would come along with an idea and say, “I want to build the first National High Temperature Surface Engineering Centre in the UK at Cranfield” and they allowed me to do that.
The aim of the centre was to have a university activity where we could produce coatings for parts which we could supply to industry for test engines. We wanted to move from just being a university research lab into being a design centre for coatings for parts for industrial manufacture - that was my dream.
The Duke of Kent at the opening of the National High Temperature Surface Engineering Centre in 2005.
The Duke of Kent at the opening of the National High Temperature Surface Engineering Centre in 2005.
What do you envision being the future areas of study or interest for you and the team?
The biggest problem at the moment is Calcia-Magnesia-Alumino Silicate (CMAS), which can come from volcanic ash or dust in the air, and which sticks to and attacks the protective coatings of engine components. At the moment that's our current programme of research as it's a big problem that is stopping industry running the engines hotter and more efficiently.
I'd like to be able to make coatings more intelligent - building self-diagnostics so that they can start to tell you when they are about to fail before they do. So that you can inspect the engine while it's in a safe condition to fly and know exactly how much life it's still got before you need to recoat or take the parts out
I'm very interested in working with the thermal barrier coatings. The coatings we're making are 200 microns thick - so the thickness of 2.5 hairs lying next to each other - and across that thickness, I want to drop 200°C.
The best we've got to is 180°C across the ceramic but that last 20°C is really hard. It's like trying to climb a mountain and then you you've got to walk the last bit of the mountain in your bare feet.
If I did that, I would save another percentage point on fuel and probably something like another £25 million a year in fuel saving for the engine operation, I can increase the life of the engine, run the engine hotter and take all that thermal load just across this ceramic.
Going forward, the next challenge will be burning hydrogen in engines. This changes the problems we have to solve because it produces a lot more water vapour and high temperature steam. There will need to be another generation coatings and TBCs to design, and that will keep my interest going for the future.
How do you ensure a work-life balance?
In 2014, I was head of the Surface Engineering and Nanotechnology Institute at Cranfield and had been doing that for about two years when I had a heart attack. One outcome of that was that I was told that I had to take things a little easier and alter my work-life balance, so I retired.
I did that for about six weeks and then was starting to miss my science so in the end I came back, did a couple of lectures for Cranfield, then got involved in a few projects, then wrote some new proposals, and since then I've been working three days a week and it seems to be my perfect work-life balance.
Outside of work, my hobby was scuba diving. I belonged to the British Sub Aqua club, which is where I met my wife. I trained to be a first-class diver and I was part of the national system of training for divers.
After the heart attack, I couldn't carry on diving so I now enjoy boating on the Grand Union Canal as a way of winding down and relaxing.
I think it’s important to keep a balance on both sides and that’s what I have at the moment, with four days to be with my family, or on the boat with my wife, and three days for me to get my science fix.
What do you think the team here at the Surface Engineering and Precision Centre and Royce at Cranfield can offer that other facilities or universities can't?
We have a number of USPs (unique selling points) but they're complementary. On the coating side, we offer access to coating equipment that other partners do not have, for example for advanced TBCs or wear resistant coatings.
We have 40 years of knowledge in how to make and design engineering coating systems.
It's having a foot in the industrial camp, so we appreciate the challenges and requirements that are needed.
On the testing side, it's our unique testing capability - in either super-hot or super-cold conditions. In other words, pushing the boundaries of where you can test to international standards and providing A-class, reliable data to the design engineers.
Overall, I've got this aim and philosophy within the centre that is we can make it, and we can break it!
We make it, and are able to analyse and characterise what we've made at the atomic level, and we control how we break it, so we understand the limits of what we've done and that allows us to make it better the next time. From the understanding that failure, we can then design the next generation of better coatings.
If we keep that loop going, we will always have first class fundamental research!
Edited by Joanna Johnson - 3rd December 2024