Making 3D printing a practical, sustainable proposition for industry
- Cranfield looked at how manufacturing from large metal forgings could be replaced by a cheaper, faster, and more sustainable process
- Cranfield brought together a package of new tooling solutions, a patented method to deliver materials with improved properties, along with tailored cost and life cycle analysis tools
- WAAM3D was set up to ensure a full supply chain for businesses, provision of technology, equipment, software, know-how training and support
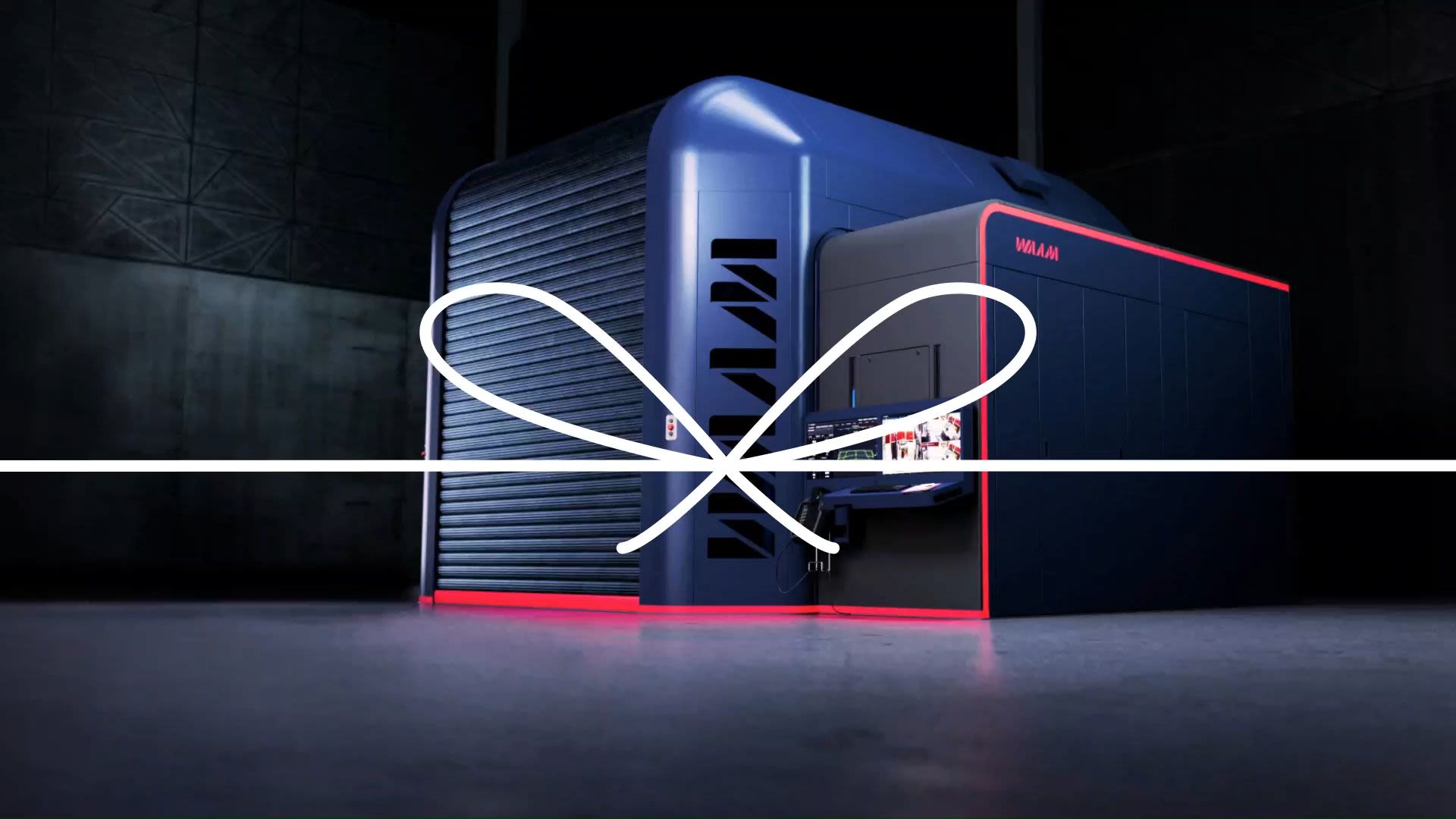
Metal 3D metal printing — or Additive Manufacturing (AM) — has typically been based on powders: slow and small-scale and still expensive. Cranfield’s Wire + Arc Additive Manufacturing (WAAM) technology has transformed the potential of metal 3D printing for industry, opening the way for major savings on energy and materials.
For aerospace and oil & gas industries, for example, research suggests savings of up to 80% in terms of the quantity needed of an energy intensive material such as titanium; along with 70% lower manufacturing costs.
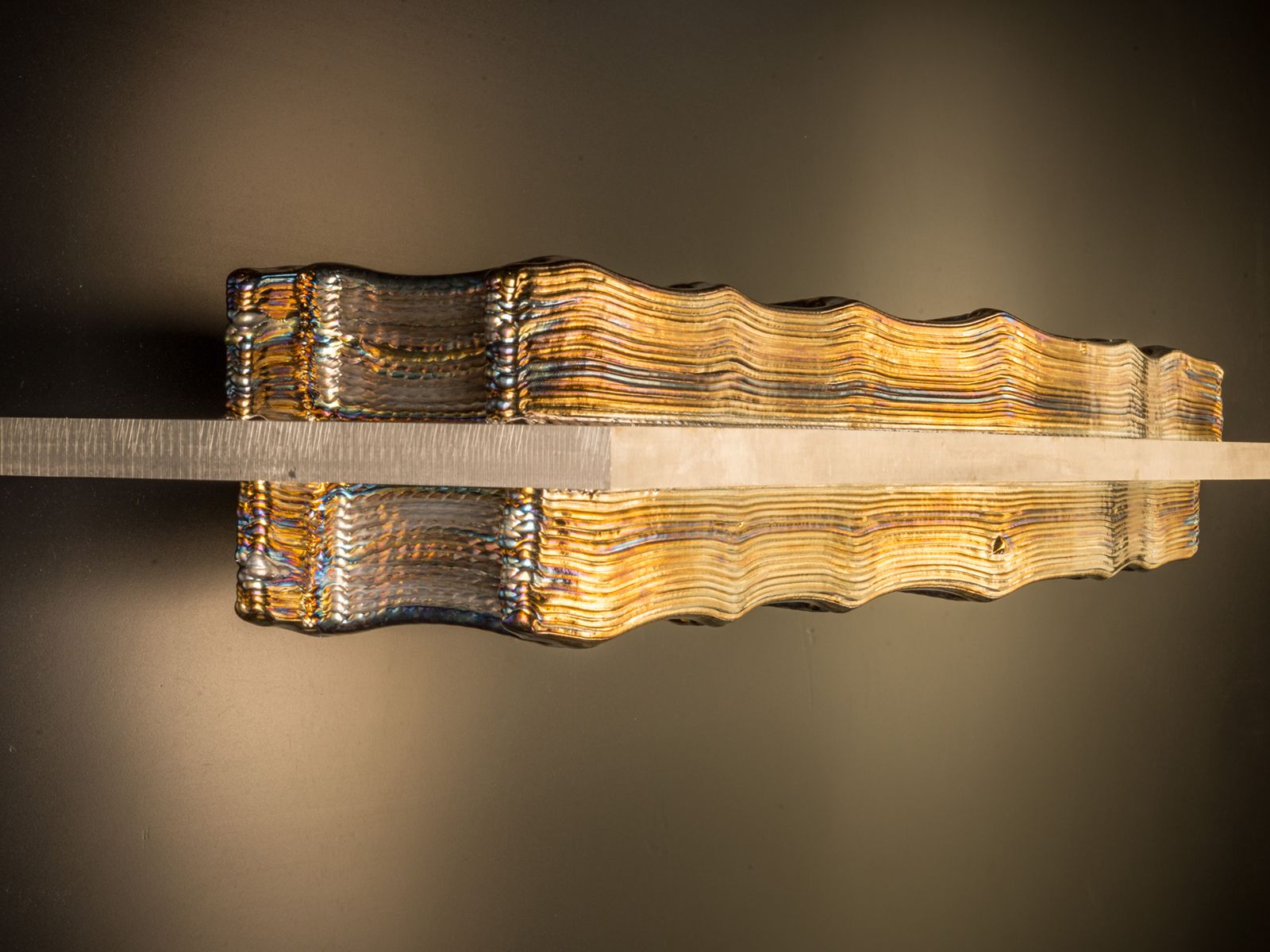
Add, don’t subtract
Traditional ‘subtractive’ methods of manufacturing lead to a great deal of waste. A typical airframe panel starts with ten or more times material than finally goes onto the actual aircraft.
This is a particular problem in terms of costs and environmental footprint given the amounts of energy involved in producing commonly used materials as titanium. Strong and lightweight, titanium demands 650 megajoules of energy per kg to produce — making it very expensive (at around $50 per kg).
Cranfield looked at how manufacturing from large metal forgings could be replaced by a cheaper, faster, and more sustainable process in terms of use of materials. That meant finding an alternative to 3D printing methods based on the use powders (with low build rates of 10-100g per hour; small build volumes typically less than 0.125m3; and weaknesses in terms of properties and integrity).
Research suggests savings of up to 80% in terms of the quantity needed of an energy intensive material such as titanium
The resulting technology, WAAM, uses an electric arc attached to the end of a robot to melt a wire and deposit molten metal in layers in a predetermined pattern. Research work was needed to explore how the full range of complexities involved with producing large-scale components (critical to the safety of an aircraft, piece of equipment or other kinds of engineered asset) could best be managed. This included combining the needs for both speed and accuracy; ensuring guaranteed structural integrity; and being cost effective to ensure there was a robust business case.
To deliver a practical solution for industry, Cranfield brought together a package of new tooling solutions, a patented method (using in-process cold work between every deposited layer) to deliver materials with improved properties, along with tailored cost and life cycle analysis tools. A spinout WAAM3D company was set up to ensure a full supply chain for businesses, provision of technology, equipment, software, know-how training and support.
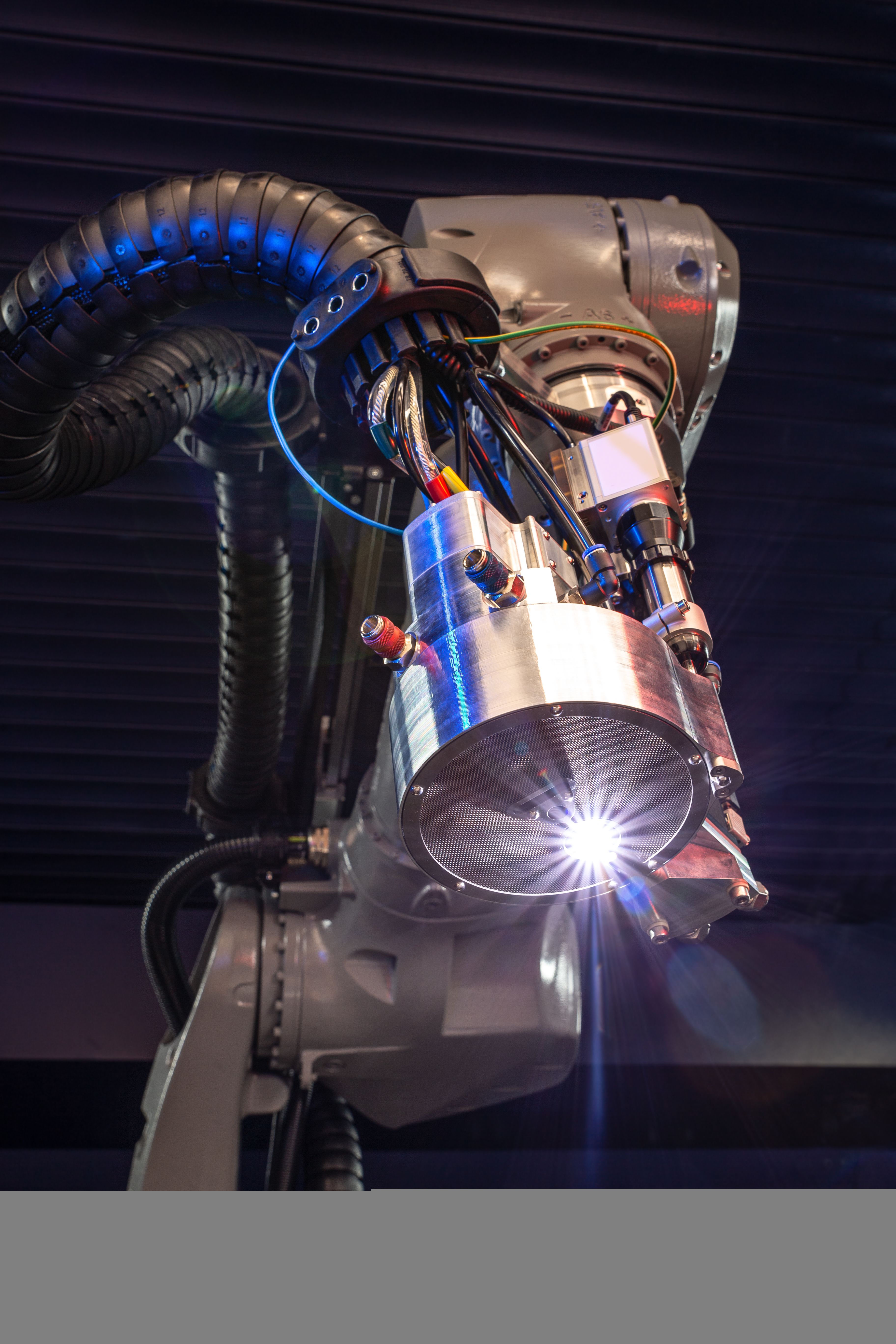
3D ecosystem
WAAM3D, working from premises in Milton Keynes, has set up a complete ecosystem for companies: turnkey systems with software for path planning and digital quality control that allow businesses to take full advantage of the new technology. Achieving £3 million in sales within the first six months of operations, the company now employs 30 people and has two facilities.
Systems and components have been used by, Thales Alenia Space, GE, Airbus Defence and Space, Aircraft Research Association, TechnipFMC and Weir amongst others.
This innovative research at Cranfield University has also led to companies in various industry sectors assessing WAAM technology for industrial engineering structural applications.
Lockheed Martin UK (LMUK) has installed a WAAM facility, with the assistance of the University, for use in a number of projects; achieving substantial reductions in lead times for parts manufacturing. As a result, LMUK customers have contracted the organisation to build parts and components for them using their WAAM cell.
TechnipFMC (an energy company), have installed several systems at their site in Dunfermline, saving significant time and costs, and proving the technology’s ability to able to deliver urgently-needed, critical parts within four and a half days — as opposed to the two-month period involved with traditional forging.
A new manufacturing company, Guaranteed, has been set up by ArcelorMittal specifically to manufacture parts by WAAM technology for their own steel production plants. This has helped them deal with a persistent issue of long periods of downtime due to failed parts, as well as allowing them to make a strategic diversification into parts and component manufacture in areas such as train and rolling stock.
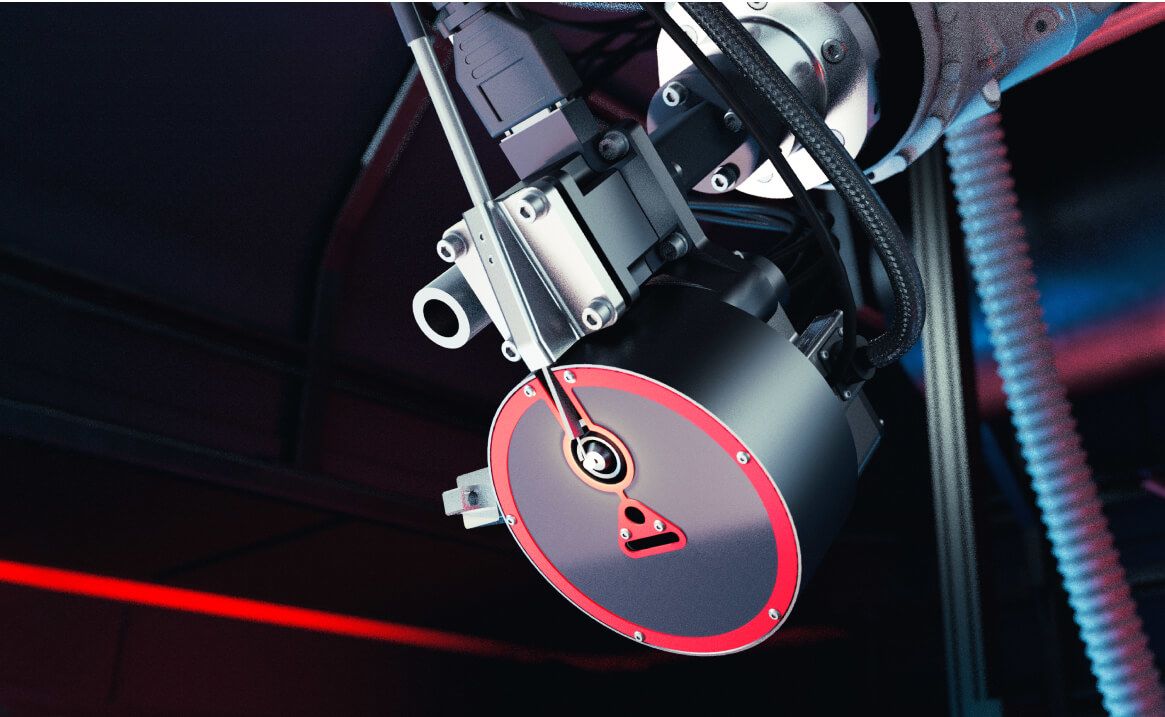
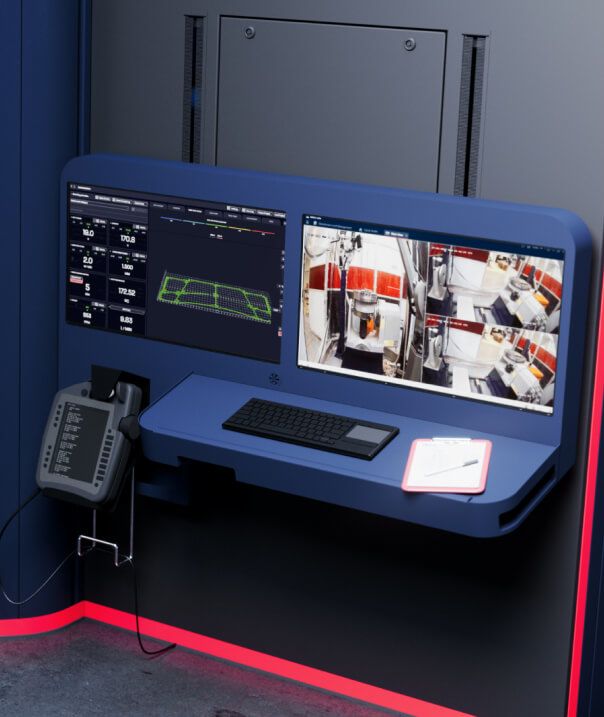
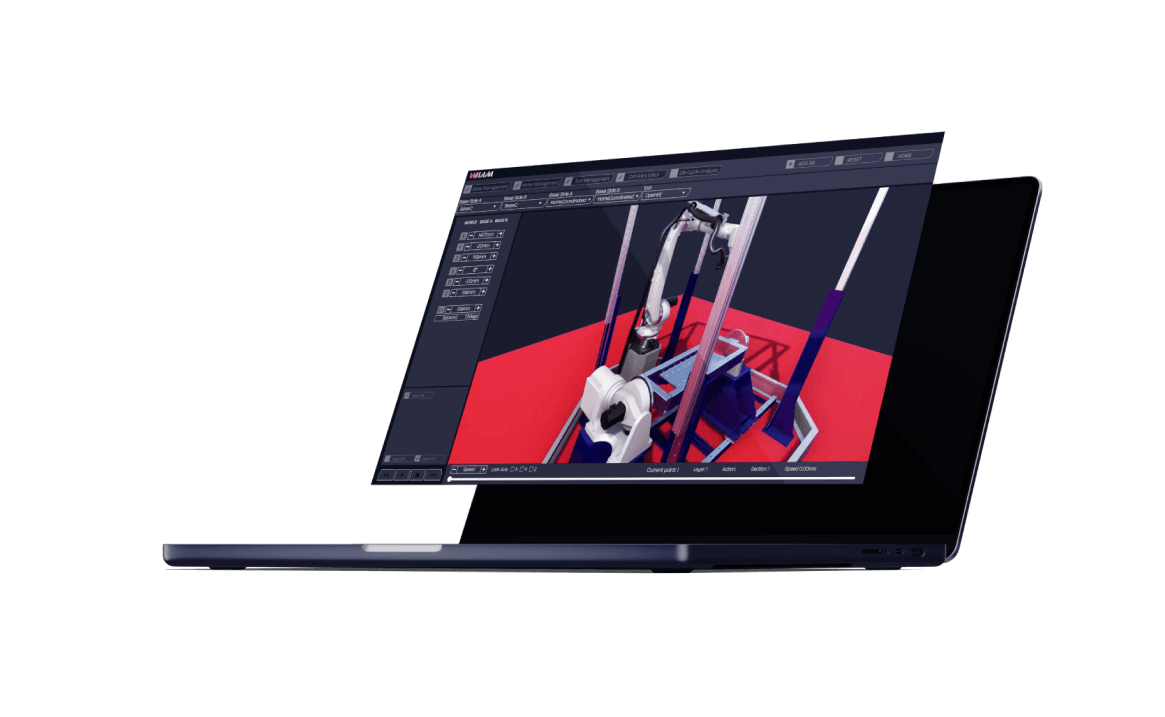
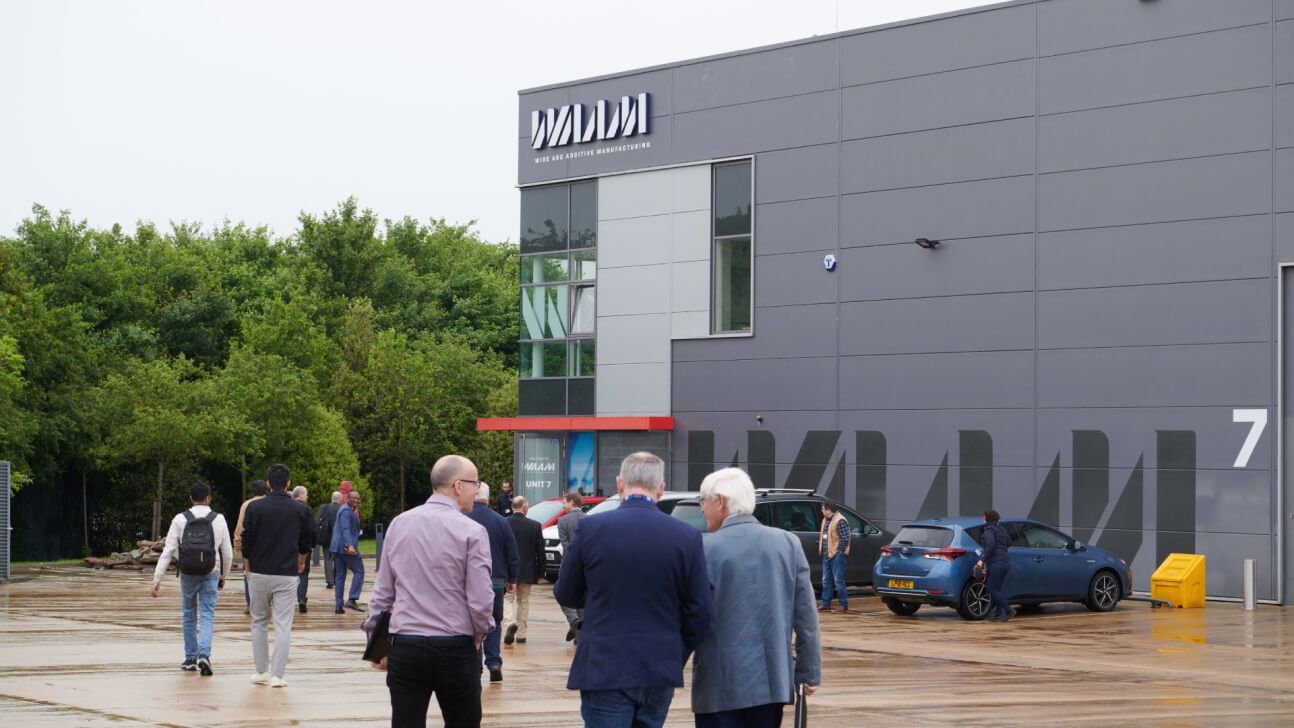
Manufacturing and Materials
We are working towards sustainable manufacturing and materials sectors through fundamental science and thought leadership for manufacturing and materials solutions across all sectors. We provide insight into current industry challenges in fields as diverse as graphene technologies, metal additive manufacturing and life cycle analysis.
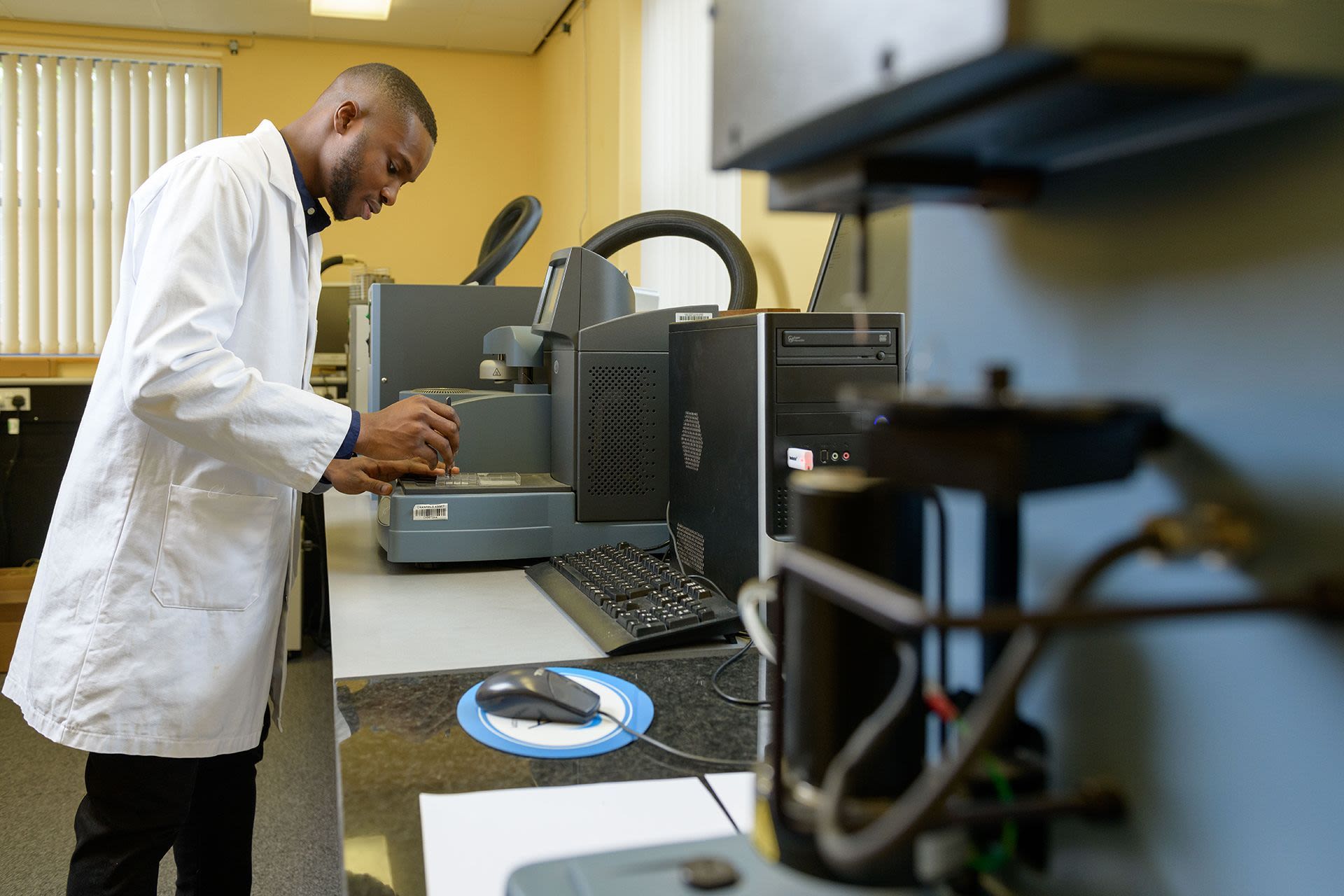
Images from Creative Commons or www.waam3d.com